Was ist Defekterkennung in der Fertigung?
dida
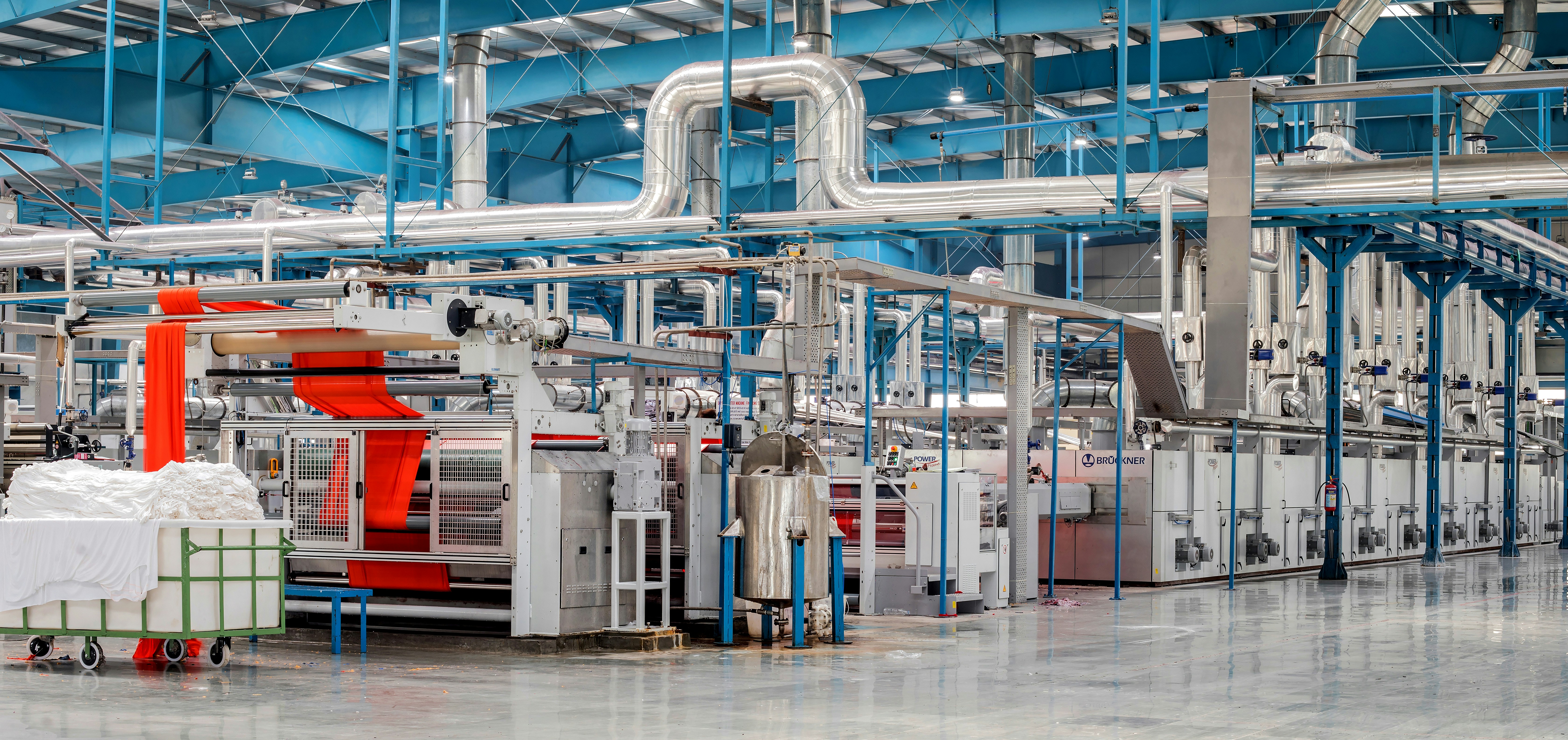
Die Defekterkennung ist ein kritischer Prozess in der Fertigung und Qualitätskontrolle, der darauf abzielt, Fehler und Unvollkommenheiten in Produkten zu erkennen, bevor sie den Verbraucher erreichen. Indem sie sicherstellen, dass nur qualitativ hochwertige Produkte die Produktionslinie verlassen, tragen Defekterkennungssysteme dazu bei, den Ruf der Marke zu wahren und den Ausschuss zu verringern. Dieser Prozess ist in verschiedenen Branchen wie der Elektronik-, Automobil-, Pharma- und Konsumgüterindustrie, in denen Präzision und Zuverlässigkeit von größter Bedeutung sind, von entscheidender Bedeutung.
Warum ist sie für die Qualitätskontrolle wichtig?
Nach Angaben des Systems Sciences Institute von IBM können die Kosten für die Behebung eines nach der Produktion festgestellten Fehlers vier- bis fünfmal höher sein als die Kosten für einen in der Entwurfsphase festgestellten Fehler und bis zu 100-mal höher als für einen in der Wartungsphase festgestellten Fehler.
Die rechtzeitige Erkennung von fehlerhaften Komponenten ist ein entscheidender Aspekt der Qualitätssicherung, der führende Hersteller von mittelmäßigen unterscheidet. Durch die schnelle Erkennung und Behebung von Mängeln während des Produktionsprozesses können Unternehmen ihre Produktionsstandards erheblich verbessern und sicherstellen, dass nur Produkte höchster Qualität auf den Markt kommen. Dieser proaktive Ansatz spart nicht nur Geld, sondern verbessert auch die Kundenzufriedenheit und Markentreue. Hersteller, die in fortschrittliche Fehlererkennungstechnologien investieren, heben sich dadurch als Branchenführer ab, die sich zu Spitzenleistungen und Zuverlässigkeit verpflichtet haben.
Wie lassen sich Fehler in der Produktionslinie erkennen?
Die Identifizierung von Produktfehlern erfordert einen systematischen Ansatz, der verschiedene Prüfmethoden und -technologien kombiniert. Bei der Sichtprüfung, die oft der erste Schritt ist, werden geschulte Mitarbeiter oder Bildverarbeitungssysteme eingesetzt, um offensichtliche Fehler zu erkennen. Zerstörungsfreie Prüfverfahren wie Ultraschall-, Magnet- und Durchstrahlungsprüfungen dringen tiefer ein, um verborgene Mängel aufzudecken, ohne das Produkt zu beschädigen.
Automatisierte Systeme, die mit künstlicher Intelligenz und Algorithmen des maschinellen Lernens ausgestattet sind, können durch die Analyse von Datenmustern subtile und komplexe Fehler erkennen. Darüber hinaus helfen statistische Qualitätskontrollverfahren, einschließlich Stichproben und Regelkarten, bei der Erkennung von Trends und Anomalien in Produktionsprozessen. Im Folgenden werden wir uns diese Techniken genauer ansehen und erläutern, welche davon für welchen Ansatz besser geeignet sind.
Was sind Defekterkennungstechniken?
1. Visuelles Inspektionssystem:
Die visuelle Inspektion ist eine der am häufigsten verwendeten Methoden zur Erkennung von Produktfehlern. Sie umfasst die manuelle Prüfung durch das menschliche Auge, die automatische Erkennung von Anomalien durch Kameras oder Systeme mit künstlicher Intelligenz. Menschliche Inspektoren verlassen sich auf ihre geschulten Augen, um Unregelmäßigkeiten wie Risse, Kratzer oder Fehlausrichtungen zu erkennen, die die Produktqualität beeinträchtigen könnten. Alternativ können Kameras, die mit Bildverarbeitungssoftware oder KI-Algorithmen ausgestattet sind, diesen Prozess automatisieren und so die Geschwindigkeit und Konsistenz verbessern. Ohne KI-Systeme hat die visuelle Inspektion jedoch ihre Grenzen; sie kann Mängel übersehen, die subtil sind oder sich in schwer zugänglichen Bereichen befinden. Darüber hinaus können menschliche Inspektoren im Laufe der Zeit ermüden und ihr Urteilsvermögen schwanken, was die Zuverlässigkeit des Inspektionsprozesses beeinträchtigt. Trotz dieser Herausforderungen ist die visuelle Inspektion aufgrund ihrer Zugänglichkeit, Vielseitigkeit und Fähigkeit, sichtbare Fehler effizient zu erkennen, von unschätzbarem Wert für die Qualitätskontrolle.
2. Zerstörungsfreie Prüfung (ZfP):
Die zerstörungsfreie Prüfung (ZfP) ist eine Methode, mit der die Struktur und die Eigenschaften eines Produkts untersucht werden, ohne seine Integrität zu verändern. Sie nutzt physikalische Phänomene wie Schall, Licht, Magnetismus, Elektrizität oder Strahlung, um Defekte aufzuspüren, die möglicherweise verborgen oder für eine Sichtprüfung unzugänglich sind. Darüber hinaus kann die zerstörungsfreie Prüfung verschiedene Merkmale wie Dicke, Härte, Dichte und Zusammensetzung messen und so einen umfassenden Einblick in die Produktqualität und -leistung geben. Diese Vielseitigkeit macht die zerstörungsfreie Prüfung unentbehrlich in Branchen, in denen Präzision und Zuverlässigkeit von größter Bedeutung sind, um sicherzustellen, dass die Produkte den strengen Qualitätsstandards entsprechen, bevor sie auf den Markt kommen.
3. Statistische Prozesskontrolle (SPC):
Die statistische Prozesskontrolle (SPC) nutzt statistische Werkzeuge und Techniken zur Überwachung und Steuerung von Qualität und Variabilität in Fertigungsprozessen. Durch die Analyse von Daten im Zeitverlauf identifiziert SPC abnormale oder instabile Bedingungen, die zu Fehlern führen können, wie z. B. Verschiebungen, Trends, Zyklen oder Ausreißer. Dieser proaktive Ansatz ermöglicht es den Herstellern, rechtzeitig Maßnahmen zu ergreifen, um eine gleichbleibende Produktqualität zu gewährleisten und das Risiko zu minimieren, dass Fehler den Kunden erreichen.
4. Versuchsplanung (DOE):
Die Versuchsplanung (Design of Experiments, DOE) ist nützlich für Forscher und Ingenieure, die Prozesse systematisch optimieren und die Produktqualität verbessern wollen. Durch die methodische Planung und Durchführung von Experimenten hilft DOE bei der Ermittlung von Schlüsselfaktoren, die einen Prozess oder ein Produkt beeinflussen, und deren Wechselwirkungen. Dieser Ansatz ermöglicht die effiziente Untersuchung mehrerer Variablen unter kontrollierten Bedingungen und führt zu Erkenntnissen, die Leistung, Zuverlässigkeit und Effizienz verbessern können. DOE ist besonders wertvoll in Branchen wie der Fertigung, dem Maschinenbau und der Pharmazie, wo eine präzise Kontrolle der Variablen entscheidend ist, um die gewünschten Ergebnisse zu erzielen und Fehler zu minimieren.
5. Maschinelles Lernen und Computer Vision
Das maschinelle Lernen, mit der Computer Vision als entscheidender Teilkomponente, hat die Fehlererkennung durch den Einsatz fortschrittlicher Algorithmen zur Analyse großer Datenmengen erneuert. Diese Algorithmen können subtile Muster erkennen, die auf Produktfehler hinweisen.
Durch das Trainieren neuronaler Netze auf kommentierten Datensätzen können Bildverarbeitungssysteme Anomalien erkennen, die traditionellen Methoden möglicherweise entgehen, und so die Genauigkeit und Effizienz in Branchen wie der Fertigungs-, Elektronik- und Automobilindustrie verbessern. Diese Algorithmen werden kontinuierlich mit neuen Daten weiterentwickelt, wodurch falsch-positive Ergebnisse minimiert und die Produktqualitätssicherung insgesamt verbessert wird. Die Integration von Computer Vision in Frameworks für maschinelles Lernen rationalisiert Inspektionen, steigert die Produktivität und sorgt für eine höhere Kundenzufriedenheit durch eine robuste und genaue Fehlererkennung.
Defekterkennung bei dida
Wir bei dida sind Spezialisten für Fehlererkennung und haben in der Vergangenheit an vielen Projekten zur Fehlererkennung gearbeitet. Hier finden Sie eine Auswahl:
Ein Beispiel ist unser Projekt zur Fehlererkennung in der Fertigung, bei dem wir Fehler in der Produktion von Halbleiterlasern aufgespürt haben.
In einem anderen Projekt haben wir eine KI-Lösung für die Fehlererkennung im 3D-Druck und in der additiven Fertigung entwickelt.
Zusammen mit einigen unserer Partner haben wir auch dieses wissenschaftliche Papier zur Fehlererkennung veröffentlicht.
Unabhängig von der Methode hängt eine wirksame Fehlererkennung von einer robusten Datenerfassung ab; wenn diese Datenerfassung mit dem Bedarf an einer präzisen Beurteilung übereinstimmt, fällt die Wahl in der Regel auf maschinelles Lernen.
Für weitere Informationen über dida oder Fehlererkennung empfehlen wir Ihnen, unsere Website zu besuchen, um mehr zu erfahren und den nächsten Schritt in Richtung fehlerfreie Produktion zu machen.